Carbon fiber was born in the United States, and its high-performance basic scientific research also started there. Today, the United States is still a strong country in the production and application of high-performance carbon fiber in the world. Studying the development history of high-performance carbon fiber technology in the United States should be a reference for the technological progress and healthy development of my country's carbon fiber industry.
This article reviews the early development process of high-performance carbon fiber technology in the United States and the important research contributions of two scientists, and analyzes their experience.
1. Carbon fiber was born in the United States and began with the invention of the incandescent lamp
Carbon fiber was born as a luminous body for incandescent lamps. British chemist and physicist Sir Joseph Wilson Swan (Sir Joseph Wilson Swan, 1828-1914) invented the incandescent lamp with platinum wire as the luminous body. In order to solve the heat-insensitive problem of platinum wires, Swann used carbonized thin paper strips instead of platinum wires. Since carbon paper strips burn easily in the air, Swann basically solved this problem by evacuating the bulb. In 1860, Swann invented a semi-vacuum electric lamp with carbon paper strip as the luminous body, which was the prototype of the incandescent lamp; but the vacuum technology was immature at that time, so the lamp life was not long. At the end of the 1870s, vacuum technology had gradually matured. Swann invented a more practical incandescent lamp and obtained a patent in 1878. In 1879, Thomas Alva Edison (1847-1931) invented the incandescent lamp with carbon fiber as the luminous body. He shaped the inner bark of linden tree, jute, manila hemp and hemp, which are rich in natural linear polymers, into the required size and shape, and baked them at high temperature; when heated, these cellulose fibers composed of continuous glucose units Be carbonized into carbon fiber. In 1892, Edison's "Manufacturing of Filaments for Incandescent Electric Lamp" invented by Edison received a US patent (patent number: 470925) (Figure 1). It can be said that Edison invented the first commercial carbon fiber.
Since the raw materials are derived from natural fibers, the early carbon fibers had almost no structural strength and were easy to chip or break during use. Even as the luminous body of an incandescent lamp, its durability is not ideal. Around 1910, tungsten filaments replaced the early carbon fiber filaments. Nevertheless, many U.S. patents confirm that in the 30 years since Edison invented carbon fiber, research on improving the performance of carbon fiber has never stopped. However, these efforts have failed to improve the performance of carbon fiber to a satisfactory level. During this time, carbon fiber research has stagnated and is in a dormant period.

Fig. 1 Edison obtained the patent for the production technology of carbon fiber filament incandescent filament in 1892
2. The emergence of man-made fibers and chemical fibers provides a prerequisite for basic scientific research on high-performance carbon fiber technology in the United States
The emergence of man-made fibers and chemical fibers has introduced carbon fiber technology into the "reinvented" era. In the early 20th century, man-made fibers such as viscose (1905) and acetate (1914) appeared, especially in the middle of the 20th century, chemical fibers such as polyvinyl chloride (1931), polyamide (1936) and polyacrylonitrile (1950) appeared. Commercialization provides a prerequisite for the United States to initiate basic scientific research on high-performance carbon fiber technology.
In the mid-1950s, the American William F. Abbott (William F. Abbott) invented a method for carbonized man-made fibers to improve the performance of carbon fibers. As the principal of Carbon Wool Corporation, Abbott filed a patent application for "Method for Carbonizing Fibers" (Application No. Serials) to the US Patent Office on March 5, 1956. No. 569,391), but it is unknown whether this application has been patented. On November 12, 1959, Abbott filed the same patent application again (Serials No. 852,530). On September 11, 1962, the application was granted a US patent (Patent No. 3053775). (figure 2)
The technical point of Abbott's patent is: a processing technology for producing fiber-shaped carbon materials with high inherent density and good tensile strength. At that time, the carbon fiber would break under the action of a small mechanical force. Abbott’s invention claims that it can make the carbon density and hardness of carbon fiber higher, and keep the fiber shape from being damaged when the mechanical force acts; and the diameter is smaller, the surface is cleaner, the flexibility and elasticity are better; the fiber diameter and Performance can be designed and controlled; raw materials must be regenerated cellulose fibers and synthetic fibers such as viscose, cupra and saponified acetic acid, and natural fibers cannot be used.

Figure 2 U.S. patents obtained by Abbott
The Carbon Wool Corporation, which applied for the patent, was a company located in Ojai, California at the time. It was founded in 1955 and was later revoked by the tax department. Due to limited information, the details of the company and Abbott are still unknown.
Abbott's patent was transferred to the Barnebey-Cheney Company of the United States. In 1957, Barneyby Cheney began commercial production of cotton-based or rayon-based carbon fiber multifilament, but it could only be used to produce ropes, mats, and wadding for high temperature and corrosion resistance; its Can be used independently as activated carbon fiber for adsorption.
Since then, basic scientific research and industrialized technology research and development of high-performance carbon fiber have entered a peak period
3. The basic scientific research of high-performance carbon fiber technology was confirmed as "a chemical milestone in American history"
The National Historic Chemical Landmark in American history is an activity carried out by the American Chemical Society (ACS›) to discover and sort out chemists and chemical events with historical influence in the United States. Each regional branch declares people and events that have occurred in the region, and the American Chemical Society organizes expert assessment and identification.
GrafTech International Ltd., located in Parma, Ohio, has declared the "High Performance Carbon Fibers" project to the American Chemical Society. The company's predecessor was Union Carbide Corp. (Union Carbide Corp.). On September 17, 2003, the American Chemical Society confirmed that the high-performance carbon fiber technology research carried out by the former US Union Carbide Corp.'s Parma Technical Center was a "chemical milestone in American history." "; Roger Bacon discovered in 1958 "graphite whiskers" and its super high-strength phenomenon; Leonard S. Singer invented the middle in 1970 Phase pitch-based carbon fiber preparation technology; they created the scientific and technological foundation of carbon fiber reinforced composite materials and are pioneers in this field. (Picture 3, Picture 4)

Figure 3. At the 2003 "Chemical Milestones in American History" award ceremony, Nina McClelland, President of the American Chemical Society, awarded the medal for the discovery of high-performance carbon fibers to Leonne, Director of the Research and Development Department of Greft International Lionel Batty
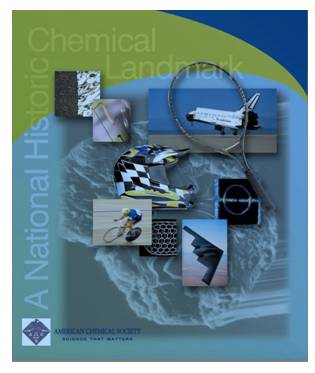
Figure 4. The cover of the memorial booklet used in the ceremony of the American Chemical Society awarding high-performance carbon fiber research "Chemical Milestone in American History"
4. Scientists at the Parma Technology Center pioneered basic scientific research on high-performance carbon fiber technology
At the end of the 19th century, the streets of American cities were illuminated by arc lamps. This lamp consists of two carbon electrodes connected to a power source. The charged particles sparkle between the two electrodes to release heat, forming an electric arc and releasing a strong light. In 1886, the National Carbon Company (National Carbon Company) was founded, marking the beginning of the synthetic carbon industry in the United States. Its earliest product was carbon electrodes for arc lamps. In 1917, the National Carbon Material Company and Union Carbide Corp. merged to form Union Carbide & Carbon Corp. (Union Carbide & Carbon Corp.). In 1957, the United States Union Carbide and Carbon Products Group changed its name to Union Carbide Corp. (Union Carbide Corp.). At the end of the 1970s, Union Carbide formed an independent division to produce carbon fiber, which was later sold to Amoco Corporation and then to Cytec Industries Inc. ). In 1995, Union Carbide Corporation established UCAR Carbon Company (UCAR Carbon Company); in 2002, it was renamed as Greft International Corporation.
In the late 1950s, Union Carbide Corporation established the Parma Technical Center in Cleveland for basic scientific research. The center is a popular university-style corporate labs in the 1940s and 1950s. Its environment is simple and modern, and its management atmosphere is free and relaxed. It has gathered many young and energetic scientists with different academic backgrounds. Research.
(1) Roger Bacon discovered "Perfect Graphite", laying the scientific foundation for high-performance carbon fiber technology
The basic scientific research of high-performance carbon fiber technology started in 1956.
In 1955, Roger Bacon (Roger Bacon, 1926–2007) (Figure 4) received a PhD in solid state physics from Case Institute of Technology. In 1956, he joined the Parma Technical Center until 1986.
Initially, the goal of Bacon’s research was to measure the temperature and pressure at the triple point of carbon (the thermodynamic equilibrium point of solid, liquid, and gas), which required nearly 100 atmospheres (atm) and 3900 degrees Kelvin (K, about 3626.85). °C). The experimental device he used is the same as the earlier carbon arc lamp, except that the operating pressure is higher. During the research, he discovered that when the pressure is low, the gaseous carbon on the negative electrode of the DC arc furnace grows into stalagmite-like filaments. These filaments are the graphite whiskers embedded in the sediment in the form of straws. Graphite whiskers are 1 inch (2.54 cm) long and have a diameter of only one-tenth of a human hair. However, they can withstand bending and kinking without being brittle, and their characteristics are amazing.
In 1960, Bacon published a paper on this in the Journal of Applied Physics, which became a milestone in the history of basic research on high-performance carbon fiber technology. Bacon believes that graphite whisker is a graphite polymer, a pure form of carbon, with carbon atoms arranged in hexagonal flakes; it is a rolled graphite flake, in which the c-axis of crystallography is exactly perpendicular to The axis of rotation; the cross-section of the cylinder is round or oval. In an argon atmosphere, at 92atm, 3900K (Kelvin, about 3626.85°C), graphite whiskers can be made. Its tensile strength, elastic modulus and room temperature conductivity are respectively 20GPa, 700GPa and 65μΩ·cm, which are similar to single crystals. Therefore, although it is not a single crystal, it exhibits single crystal properties along the filament axis. In 1960, Bacon’s discovery of graphite whiskers received a US patent (patent number: 2957756) (Figure 5). At the time, Bacon believed that the preparation of graphite whiskers was only a laboratory result, and there was still a long way to go to use its principles to produce practically valuable carbon fibers.
The next ten years of research is to obtain low-cost, high-efficiency production of high-performance carbon fiber technology with graphite whisker characteristics.

Figure 5 The patents obtained for the technological invention of the discovery and preparation of graphite whiskers by Roger Bacon
Sixty years after discovering graphite whiskers and their characteristics and inventing the method for preparing graphite whiskers in the laboratory, on October 25, 2016, Roger Bacon was elected to the National Inventors Hall of Fame. (Image 6)

Figure 6. Roger Bacon inducted into the National Inventors Hall of Fame
(2) Advances in high-strength and high-modulus carbon fiber technology and early commercial applications
In 1959, scientists at the Parma Technology Center invented the preparation technology of high-performance rayon-based carbon fibers. Gary Ford (Curry E. Ford) and Charles Mitchell (Charles V. Mitchell) invented the process technology of heat-treating rayon at a high temperature of 3000°C to produce carbon fiber, and produced the strongest commercial carbon fiber at the time. Obtained a patent (patent number: 3107152) (Figure 7). The U.S. Air Force Materials Laboratory (U.S. Air Force Materials Laboratory) soon adopted this rayon-based carbon fiber as a phenolic resin reinforcement and developed a composite material for the thermal shield of spacecraft. Its function is that when returning to the atmosphere, the shell of the missile or rocket will violently rub against the atmosphere, and the surface will form a high temperature. The phenolic resin will slowly decompose after absorbing heat. The carbon fiber will prevent the phenolic resin from being burned, ensuring that the missile or rocket completes its journey in the atmosphere. In 1963, a substantial breakthrough was made in the research of carbon fiber reinforced resin composite material technology, and the composite material technology entered the era of "advanced composite materials". Previously, the reinforcement of resin-based composite materials has been monopolized by glass fibers and boron fibers. Compared with glass fiber and boron fiber, carbon fiber as a reinforcement has better cost performance.

Figure 7 Gary Ford's invention patent of fibrous graphite
In 1964, Wesley A. Schalamon (Wesley A. Schalamon) and Roger Bacon jointly invented the technology for the commercial manufacture of high modulus rayon-based carbon fibers; “hot-stretching (hot-stretching) at high temperatures above 2800°C )” Rayon makes the orientation of the graphite layer almost parallel to the axis of the fiber; the key to the technology is to stretch the fiber during heating, rather than stretching after reaching a high temperature. This process increases the fiber modulus by 10 times and is a key step in preparing carbon fibers with the same properties as graphite whiskers. At the end of 1965, the Thornel 25 carbon fiber manufactured by this technology was put on the market. In the following 10 years, Union Carbide Corporation of the United States developed a series of high-modulus carbon fibers using high-temperature thermal drawing technology. The modulus of the Thornel series products reached 830GPa. This invention by Salmon and Bacon was patented in 1973 (patent number: 3716331) (Figure 8).

Figure 8 The invention patent for the preparation process of Wesley Salmon high modulus carbon fiber
(3) Leonard Singer invented mesophase pitch-based graphite fiber manufacturing technology
In the process of high temperature heat treatment, the internal structure of the material will change from disorder to order. Carbon-containing substances can be carbonized into carbon materials with a carbon content of about 99% at 1000°C; at 2500°C, they can be carbonized into carbon materials with a carbon content of 100%. However, not all carbonaceous materials can get real graphite after high temperature heat treatment. Only those carbonaceous materials with a sufficiently orderly structure that can form graphite whiskers can be processed into pure graphite with high thermal conductivity, high electrical conductivity and high hardness through high temperature heat treatment. Polyacrylonitrile and rayon do not belong to this type of carbonaceous material, so it is impossible to make graphite fibers through high temperature heat treatment. To make carbon fiber with higher performance, a new material is necessary as a precursor.
Leonard S. Singer (1923-2015, Figure 9) opened the way for this. In the mid-1950s, Singer received his Ph.D. from the University of Chicago and joined the Parma Technology Center to engage in electron spin resonance research.
Although he has no experience in carbon or graphite research, he tried to study the mechanism of carbonization. Heating raw materials such as petroleum and coal produces pitch-like substances. Petroleum-based and coal-based pitch are the basic raw materials for manufacturing carbon and graphite products. Asphalt contains more than 90% carbon, much higher than rayon and acrylonitrile. They are a complex mixture of hundreds of aromatic hydrocarbons with a wide molecular weight distribution, and they are important precursors with high carbon content. At the same time, studies have shown that most of the substances in this type of mixture are isotropic, and through further polymerization, the molecules can be oriented in a layered form.
In 1970, Singer solved the key technology of preparing high modulus pitch-based carbon fiber; the core of its technology is that liquid crystal or mesophase is the key to achieving high model performance. 80-90% of the weight of the mesophase pitch can be converted into carbon, and it has excellent thermal conductivity, electrical conductivity, oxidation resistance, and low thermal expansion rate. He successfully processed the raw material pitch into mesophase or liquid crystal pitch, and then achieved orientation through flow and shear. Singer and assistant Allen Cherry (Allen Cherry) designed a "taffy-pulling" machine and used it to apply tension to the viscous mesophase pitch to reorder the molecules, and then perform Heat treatment. The technology was successful, and they made highly oriented graphite fibers. In 1975, Union Carbide began commercial production of continuous filaments of the Thornel P-SS grade; in 1980-82, its modulus reached 690-830GPa. In 1977, Singh obtained a patent for graphite fiber and its manufacturing process (patent number: 3919387) (Figure 10). The US Air Force Materials Laboratory (AFML) and the US Navy (NSSC) funded Singer’s research.

Although he has no experience in carbon or graphite research, he tried to study the mechanism of carbonization. Heating raw materials such as petroleum and coal produces pitch-like substances. Petroleum-based and coal-based pitch are the basic raw materials for manufacturing carbon and graphite products. Asphalt contains more than 90% carbon, much higher than rayon and acrylonitrile. They are a complex mixture of hundreds of aromatic hydrocarbons with a wide molecular weight distribution, and they are important precursors with high carbon content. At the same time, studies have shown that most of the substances in this type of mixture are isotropic, and through further polymerization, the molecules can be oriented in a layered form.
In 1970, Singer solved the key technology of preparing high modulus pitch-based carbon fiber; the core of its technology is that liquid crystal or mesophase is the key to achieving high model performance. 80-90% of the weight of the mesophase pitch can be converted into carbon, and it has excellent thermal conductivity, electrical conductivity, oxidation resistance, and low thermal expansion rate. He successfully processed the raw material pitch into mesophase or liquid crystal pitch, and then achieved orientation through flow and shear. Singer and assistant Allen Cherry (Allen Cherry) designed a "taffy-pulling" machine and used it to apply tension to the viscous mesophase pitch to reorder the molecules, and then perform Heat treatment. The technology was successful and they made highly oriented graphite fibers. In 1975, Union Carbide began commercial production of continuous filaments of the Thornel P-SS grade; in 1980-82, its modulus reached 690-830 GPa. In 1977, Singh obtained a patent for graphite fiber and its manufacturing process (patent number: 3919387) (Figure 10). The US Air Force Materials Laboratory (AFML) and the US Navy (NSSC) funded Singer’s research. Figure 10 Leonard Singer's patent for preparing pitch fiber with high mesophase content
Although asphalt is a relatively cheap raw material, the cost of carbon fiber made from it varies greatly. Low modulus, non-graphitized, cheaper mesophase pitch-based carbon fiber, used to make aircraft brake pads and reinforced cement. The mesophase pitch-based graphite fiber, which has high-end properties such as ultra-high modulus and ultra-high thermal conductivity and is expensive, is used to manufacture key components such as rocket nozzle throat lining, missile nose cone and satellite structure. It is the key to irreplaceability. Aerospace materials.
5. The miss and return of U.S. polyacrylonitrile-based carbon fiber technology
Rayon, polyacrylonitrile or pitch are the three major precursors of carbon fiber. Among them, the comprehensive performance of acrylonitrile-based carbon fiber (Polyacrylonitrile ‹PAN›-based Carbon Fibers) is particularly outstanding, and it has replaced rayon-based carbon fiber in many fields. The reason why carbon fiber performance has been improved by leaps and bounds is the invention of better acrylic fiber. Scientists in the United Kingdom and Japan first developed pure acrylonitrile polymers. During processing, the continuous carbon and nitrogen atoms in the molecular chain can form a highly oriented graphite-like layer, thereby reducing the need for thermal stretching.
In 1941, the American DuPont Company invented the acrylic fiber technology. In 1950, DuPont began commercial production of acrylic fibers under the "Orlon" brand. In 1944-45, L. L. Winter of Union Carbide Company discovered that acrylonitrile did not melt at the ashing temperature and believed that it could be made into fiber-shaped carbon materials. In 1950, Houtz discovered that heat-treated acrylic fibers at 200°C in the air produced products with good fire resistance. Later, similar products were called "Black Orlon (Black Orlon)". Originally, these findings should be the starting point for the development of high-performance PAN-based carbon fiber technology, but due to excessive attention to rayon-based carbon fiber technology research, American scientists missed the development opportunity of PAN-based carbon fiber technology.
Without the knowledge of Western scientists, Japanese scientists have been silently carrying out research on PAN-based carbon fiber technology. In 1961, Akio Shindo of the Government Industrial Research Institute of Japan produced PAN-based carbon fibers with a modulus of 140 GPa in the laboratory, which was three times higher than that of rayon-based carbon fibers. Shinto Akio’s invention was quickly promoted in the scientific and industrial circles of Japan. Toray Industries developed an acrylonitrile precursor with excellent performance and established a carbon fiber pilot plant, which has since occupied the PAN-based carbon fiber. Technology leadership. In 1970, Toray Corporation of Japan signed a technical cooperation agreement with Union Carbide Corporation of the United States. The latter exchanged carbonization technology for the former's acrylonitrile precursor technology, and soon produced high-performance PAN-based carbon fibers, which brought the United States back to the United States. The forefront of carbon fiber technology.
6. Conclusion
Looking at the early development of American carbon fiber technology, the following laws and facts are worth noting:
(1) Carbon fiber was born from the product invention of electro-optical conversion device.
The mid-to-late 19th century was the period when the achievements of the scientific and industrial revolutions broke out. A large number of scientific discoveries and technological inventions emerged, contributing to the modernization of human society. Carbon fiber technology is produced in this era. In order to light up the dark night, Swann and Edison invented the electric lamp that converts electricity into light. As the luminous body of the electric lamp, carbon fiber was quietly born.
The nascent carbon fiber is not eye-catching. Because electric lights were the focus of attention at that time. Although the importance of carbon fiber has been temporarily ignored, as long as it is a vital thing, it will certainly embark on a regular process of birth, growth, maturity, decay and rebirth. Technology and products are the same as organisms.
(2) High-performance carbon fiber technology was born from scientific discoveries in basic research.
Graphite whiskers, and their characteristics and microstructure, were discovered in basic scientific research. This discovery provides a direction and goal for the research of high-performance carbon fiber manufacturing technology. In the 1950s and 1970s, the discoveries of basic scientific research and the invention of a large number of engineering technologies contributed to the maturity and improvement of high-performance carbon fiber technology.
(3) There is a "U.S.-Japan alliance" in the field of high-performance carbon fiber technology.
The reason why the Japanese scientist Akio Shinto came up with the idea of conducting carbon fiber research was inspired by reports of technological progress in this field in the United States. After the successful commercialization of PAN-based carbon fiber by Toray Corporation of Japan, it signed an agreement on the exchange of raw silk and carbonization technology with Union Carbide Corporation of the United States, enabling the two companies to have the entire process technology for high-performance carbon fiber production. Since then, other Japanese companies have also produced excellent acrylic fiber precursors. Japan's Sumitomo Corporation (Sumitomo Corporation) provided the precursor of acrylic fiber for Hercules Incorporated of the United States, and was authorized to produce carbon fiber by the British company Courtaulds PLC. 1 The technical cooperation between the United States and Japan has enabled rapid development and wide application of high-performance carbon fiber technology. Today, American Boeing aircraft use carbon fiber produced by Japan’s Toray. In 2015, Toray of Japan built a carbon fiber production plant for the entire process from acrylonitrile precursor to carbonization in the United States to meet Boeing's rapid growth in carbon fiber demand for advanced aircraft production. The technological interaction between the United States and Japan is one of the important factors that promote the continuous development of high-performance carbon fiber technology.
Wang Qiaoting
Source|Carbon Fiber Production Technology
Edit|Dr. DT Elephant
(Cooperative report|Article reprint|Submission exchange)
Statement|This article only represents the author’s point of view, not the company’s position
Column Editor
NingboThree